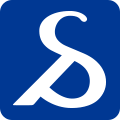
Vendor Profile
yamakiikai
Address | centrairlogisticscenter2F centrair4-11-3 Tokonameshi Aichi, JAPAN ZIP:479-0833 |
---|---|
Representative Name | HIDEYUKI ISHIDA |
Annual Revenue | closed |
No. of Employees | 22 |
Web Site URL | |
SNS |
People Also Searched
Other items from this category
SD item code:6094552
Detail | Price & Quantity | ||
---|---|---|---|
S1 |
180cc
![]()
180cc
(FY100)
|
(FY100)
Wholesale Price: Members Only
1 pc /set
In Stock
|
Dimensions |
---|
180cc
*Capacity is 70% of full water capacity. |
Specifications |
---|
Country of manufacture: Japan
Material / component: Pottery
|
Description
*Cannot be used in conjunction with other discounts or promotions, such as coupons. *Discount Offer*. 5% OFF for orders over 50,000 yen! After you place your order, we will give you a 5% discount on the purchase price. A wide variety of pottery [Mino ware] is produced in Gifu Prefecture*Higashi Mino. Mino ware is supported by a long history and tradition, Mino ware, which is supported by a long history and tradition, accounts for about 60% of the national market share in terms of tableware production, It is no exaggeration to say that it is the representative of Japanese pottery. Mino ware is used casually in daily life and blends in without being noticed. That is [Mino ware]. The history of Mino ware is old and dates back to more than 1,300 years ago. At first, the technique of Sue ware was introduced from the Korean peninsula. In the Heian period (10th century), ash-glazed ceramics known as shirashi (white porcelain) began to be fired. Shirashi, or white porcelain with an ash glaze, began to be fired during the Heian period (10th century). Shirashi was an improved version of Sue ware with a glaze. At this time, the number of kilns increased and the area became a full-fledged pottery production center. From the Azuchi-Momoyama period to the early Edo period (1603-1867), pottery reflecting the tastes of tea ceremony masters became popular along with the tea ceremony. pottery reflecting the tastes of tea masters was produced. In the early Showa period (1926-1989), the demand for high-end products increased, and the technology improved markedly along with increasing mechanization. The kilns were also changed from charcoal kilns to heavy oil kilns. Kilns were also changed from charcoal kilns to heavy oil kilns* to shuttle gas kilns* to tunnel kilns, roller hearth kilns, and roller hearth kilns. Tunnel kilns and roller hearth kilns were developed at the same time, Improved yield * Uniformity of products * Mass production Fortunately, Mino ware has not been hit by war and has survived many recessions, Mino ware, which fortunately did not suffer from war and has survived many recessions, is now by far the largest producer in Japan, both in name and reality. Western tableware accounts for about 51% of domestic production, Japanese tableware for about 58%, and tiles for about 41%. Mino ware accounts for the majority of tableware used in Japan. |
More
Shipping Method | Estimated Arrival |
---|---|
Sea Mail | From Feb.3rd to Apr.7th |
Air Mail | From Jan.16th to Jan.20th |
EMS | From Jan.15th to Jan.20th |
Pantos Express | From Jan.17th to Jan.22nd |
DHL | From Jan.15th to Jan.17th |
UPS | From Jan.15th to Jan.17th |
FedEx | From Jan.15th to Jan.17th |
Some trading conditions may be applicable only in Japan.
*Safety*Security: The product has passed the lead*cadmium test.
*Please cooperate with us to sell the product at the regular price. Made in Japan f1101m964g1023l925y1214 |
Other items from this category:
*Discount Offer*.
5% OFF for orders over 50,000 yen!
After you place your order, we will give you a 5% discount on the purchase price.
A wide variety of pottery [Mino ware] is produced in Gifu Prefecture*Higashi Mino.
Mino ware is supported by a long history and tradition,
Mino ware, which is supported by a long history and tradition, accounts for about 60% of the national market share in terms of tableware production,
It is no exaggeration to say that it is the representative of Japanese pottery.
Mino ware is used casually in daily life and blends in without being noticed.
That is [Mino ware].
The history of Mino ware is old and dates back to more than 1,300 years ago.
At first, the technique of Sue ware was introduced from the Korean peninsula.
In the Heian period (10th century), ash-glazed ceramics known as shirashi (white porcelain) began to be fired.
Shirashi, or white porcelain with an ash glaze, began to be fired during the Heian period (10th century).
Shirashi was an improved version of Sue ware with a glaze.
At this time, the number of kilns increased and the area became a full-fledged pottery production center.
From the Azuchi-Momoyama period to the early Edo period (1603-1867), pottery reflecting the tastes of tea ceremony masters became popular along with the tea ceremony.
pottery reflecting the tastes of tea masters was produced.
In the early Showa period (1926-1989), the demand for high-end products increased, and the technology improved markedly along with increasing mechanization.
The kilns were also changed from charcoal kilns to heavy oil kilns. Kilns were also changed from charcoal kilns to heavy oil kilns* to shuttle gas kilns* to tunnel kilns, roller hearth kilns, and roller hearth kilns.
Tunnel kilns and roller hearth kilns were developed at the same time,
Improved yield * Uniformity of products * Mass production
Fortunately, Mino ware has not been hit by war and has survived many recessions,
Mino ware, which fortunately did not suffer from war and has survived many recessions, is now by far the largest producer in Japan, both in name and reality.
Western tableware accounts for about 51% of domestic production, Japanese tableware for about 58%, and tiles for about 41%.
Mino ware accounts for the majority of tableware used in Japan.
◆◆◆割引特典◆◆◆
ご注文金額5万円以上で5%OFFいたします!
ご注文後、ご購入金額に対して5%を割引きいたします。
岐阜県・東美濃で生産される多種多様な焼物『美濃焼』。
長い歴史と伝統に支えられた美濃焼は、
食器類の生産が全国シェアの約60%を占めており、
日本の焼物の代表といっても過言ではありません。
日常生活の中で何気なく使われ、知らないうちに溶け込んでいる焼物。
それが『美濃焼』です。
美濃焼の歴史は古く、今から1300年以上前まで遡ります。
最初は朝鮮半島から須恵器の技術が伝えられました。
平安時代(10世紀)になると白瓷と言われる灰釉を施した
陶器が焼かれるようになりました。
この白瓷は須恵器を改良し、釉薬を使ったものです。
この頃から窯の数も多くなり、本格的な焼き物生産地となりました。
安土桃山時代から江戸時代初頭にかけて、茶の湯の流行と共に
茶人の好みを反映した焼き物が生産されました。
昭和初期には高級品需要も増え、益々の機械化と同時に技術も
著しく向上しました。 窯も炭窯から重油窯・シャトルのガス窯・
トンネル窯、ローラーハースキルンへと進化すると同時に、
歩留りの向上・製品の均一化・大量生産化に繋がっていきます。
幸い戦火にみまわれず、幾多の不況にもうち勝ってきた美濃焼は、
今となっては圧倒的に名実共に日本一の生産量を誇っています。
洋食器は国内生産の約51%、和食器は約58%、タイルは約41%です。
いわゆる日本で使用する食器類の過半数が美濃焼で占められています。